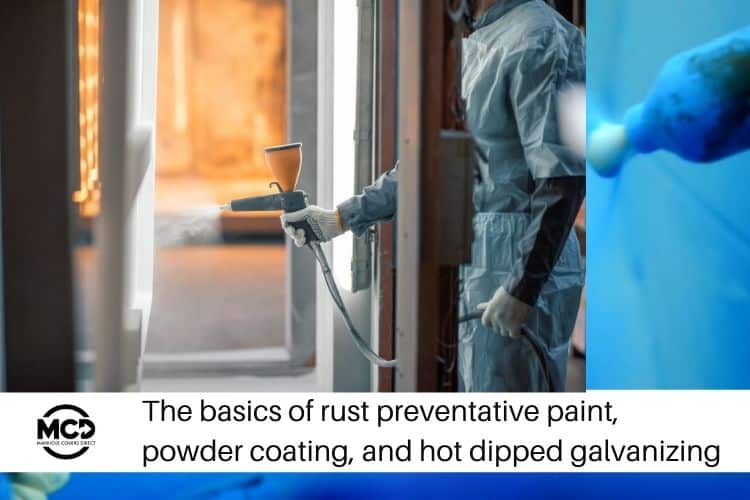
Rust preventative paint, powder coating, and hot dipped galvanizing are all important elements of industrial manufacturing, and something that you as a procurement professional should know about. Learn more about the different types of metal coating and how they impact the life of your manhole covers and other materials.
Protective coatings for metals have been around for thousands of years. Ancient people originally used oils and waxes to prevent rust on basic iron objects such as swords or axes. In 1836 Stanislas Sorel patented the galvanizing method, which involved dipping steel into zinc. Powder coating came around in 1945 when Daniel Gustin received a patent for electrostatically coating a material with powder and subsequently baking it on.
There are always questions about what method works best and how long do they last. Well, it’s the usual answer – it depends. Generally speaking, the climate, use and general maintenance play a huge part in how long these coatings last and where they are applied.
We can start with Rust Preventative Paint. Rust preventative paint has several benefits: Ease of application, quicker lead times and it’s inexpensive. However, there are always drawbacks with budget solutions. Rust preventative paint will prevent rust but it can be easily damaged and erodes quickly relative to other coatings. Rust preventative paint must be reapplied often in high traffic, wet and corrosive environments and in high sunlight. Rust preventative paint is a good choice in areas that receive low traffic, sunlight and various other factors that can quickly wear paint thin.,
Powder Coating is a big step up from rust preventative paint. While more expensive, it offers better protection and you can choose whatever color you like. Various common goods are powder coated; steel roofs, railings and many other objects where aesthetics is important but rust prevention is also important. Powder coatings can last up to 40 years, once again depending on environment and use. Manhole covers, for example, commonly have salt, sand, UV exposure and traffic which will reduce the life of the coating. Overall, powder coating is a great choice that provides longevity and allows for color choice.
Hot-dipped galvanizing is by far the best option to prevent corrosion. Galvanizing is the process of coating steel or iron in zinc, while hot-dipped galvanizing is literally dipping the steel or iron piece in a bath of molten zinc. Zinc is more reactive than iron or steel and will actually attract the oxidation, saving the ferrous metals. A protective layer of oxide and carbonate forms as the zinc corrodes. Chain-link fences are an excellent and common example of galvanized metal that will last many years but eventually rust once the zinc has been totally exhausted. Hot-dipped galvanizing can last for up to 100 years, once again depending on the environment and traffic. It’s an excellent choice for busy areas with bad weather or conditions. However, galvanized metal doesn’t come in more than one color: metallic zinc.
When it comes to corrosion prevention, a surface coating is a must. Manhole Covers Direct can provide any of the three options for a large catalog of products. The best option will invariably consist of many considerations such as traffic, cost, color, finish, environment and other factors. Regardless, Manhole Covers Direct is happy to provide the best service for the best product.